There’s nothing quite like the day when fall weather first hits. Sitting on your porch, a warm coffee in hand, watching colorful leaves fall gently from the trees, curling up in your favorite sweater with a knitted blanket sitting on your knees. Sweater weather season is officially underway and it’s time to break out our cozy knits. But how did your sweaters go from manufacturing plant to warming you on breezy fall evenings?
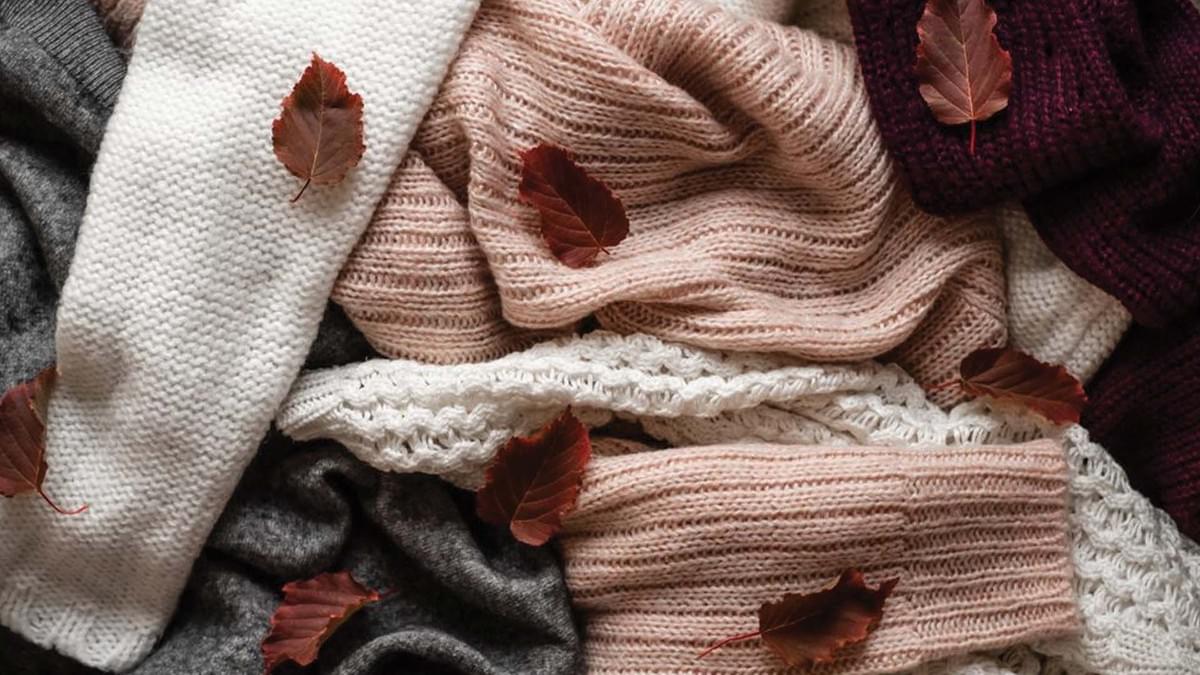
The process of creating your favorite sweater starts with the yarn. Once the yarn has been sourced, it is winded into cones using a winding machine. The yarn is then distributed to operators at manufacturing facilities. Knitters will then knit sweaters on a flat knitting machine according to a design panel.
The most popular manufacturing technique for sweaters is called the ‘cut and sew’ technique. It’s preferred because of the high rate of production and the ability to work around any defects and reduce waste. It involves a sweater being produced using the full width of the needle bed on a flat-bed machine or the full diameter of a circular machine. Using this method, several linear yards of fabric will be produced as one piece from which the various panels will be sewn and cut.
Another popular manufacturing method is referred to as ‘panel knitting’ which involves knitting specific areas of the garment referred to as ‘panels’. Then, during the knitting process, separation thread is inserted between the panels which allows them to be divided without cutting them. Finally, once the panels are knitted, the separation thread is removed.
After this, the sweater will receive a quality check utilizing the garment measurements. Then last-minute touches will be added such as linking of different panels, buttons, and trimming of loose fabrics or strings. After it is washed, ironed, and passes one last quality check it’s ready to be shipped to your favorite cozy clothing store.